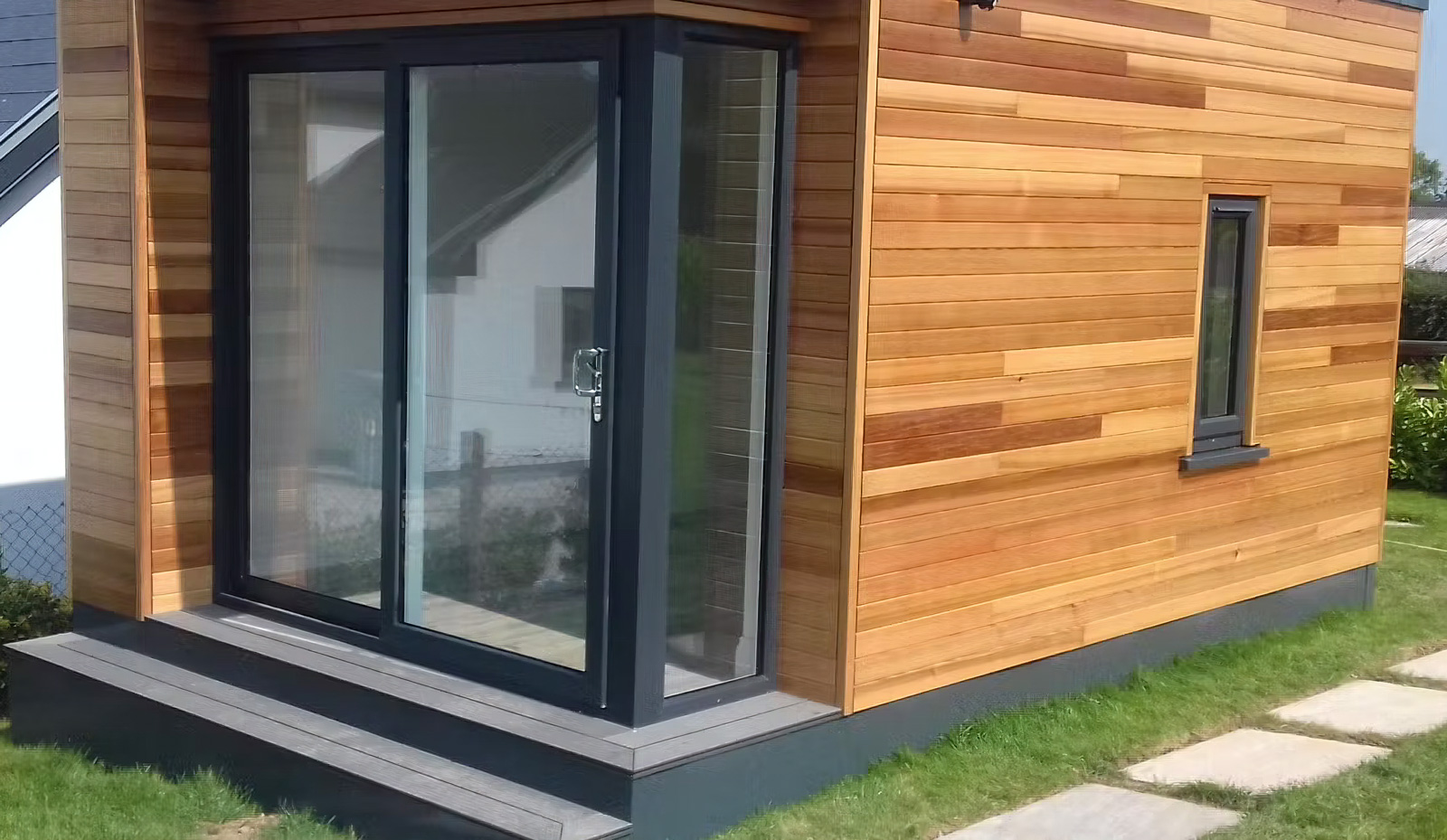
Recycling and waste management
Our waste management strategy starts with the materials and methodologies we choose to build with, after that our priority is to keep waste to a minimum.
Our Methodologies
- Off-site fabrication process.
- Considered design and measurement.
- On-going material management and storage.
- Panelised system which can be dismantled.
- Footings; Our pile system can be removed and reused, unlike a concrete base.
- A small portion of our treated timber and sheet material that goes into the waste is handled by a waste management company.
Our Materials
- Timber is non-toxic and does not break down into materials that could potentially damage the environment.
- Our Timber carcass can be disassembled at end of life and reused.
- Our Insulation which is made from recycled newspaper can be reused.
- Our footings, which are galvanised piles can be removed and reused.
Sustainable Materials
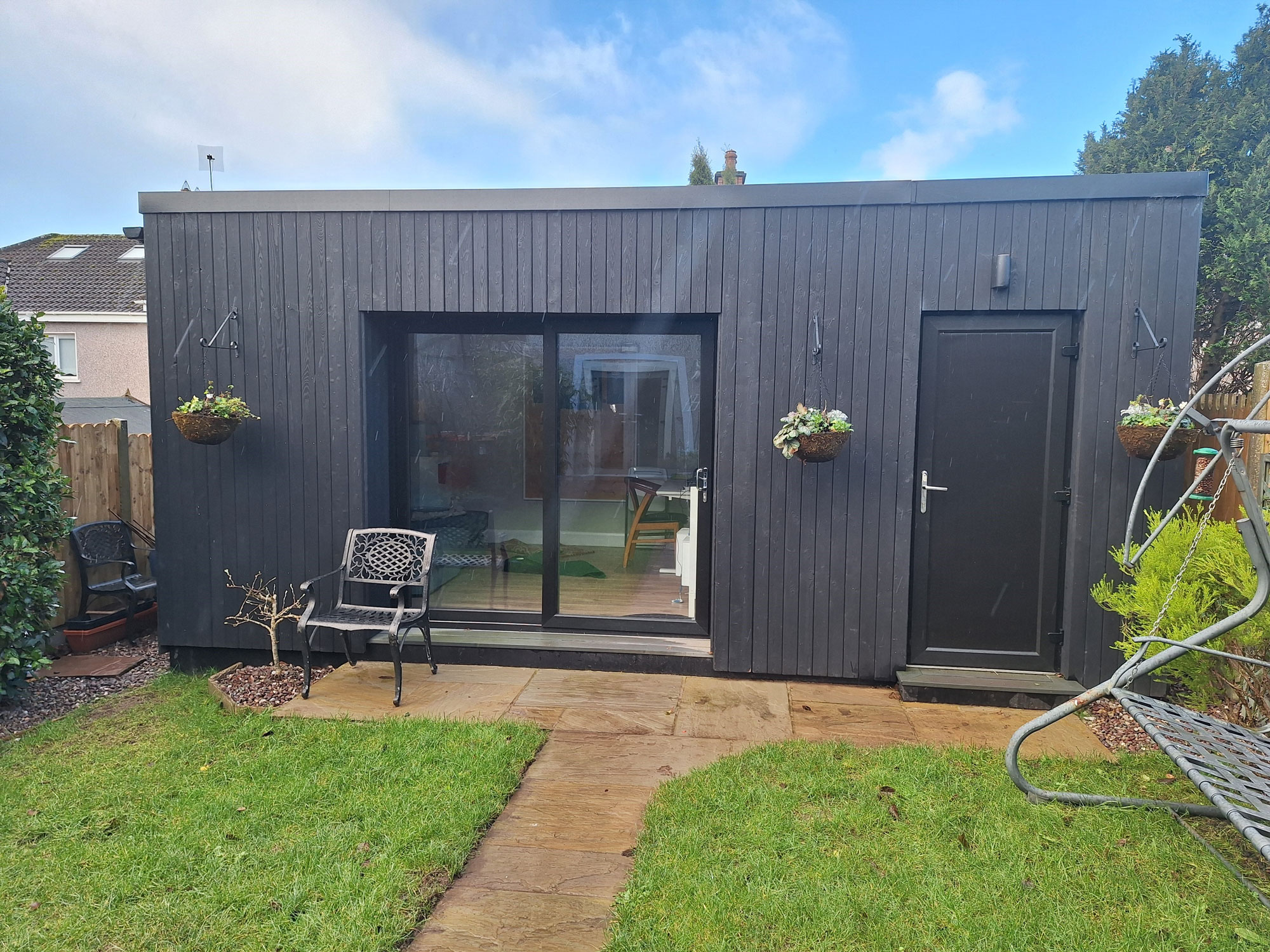
General:
Locally grown FSC certified timber is used as the main structural component and its use along with natural fibre insulation, exterior timber cladding, combine to make the whole unit a carbon ‘sink’ that locks up carbon for the life of the building.
Locally Sourced:
Our structural timber is grown in Ireland and our sheet material is also manufactured here. Our insulation is manufactured a couple of hundred yards away from our plant from recycled newspaper.
Low impact:
Our foundation pile system is low-impact and unobtrusive and the piles themselves can be reutilised at the end of the building’s life. Furthermore, very little ground is broken with this practice and almost eliminates the release of Nitrous Oxide into the atmosphere. Nitrous Oxide is responsible for 7% of global warming. This system has the added bonus of eliminating the need for concrete from the build.
Durability:
We believe longevity is crucial to sustainable building and therefore choose durable materials to build structures that will last. Our external cedar cladding has a life expectancy of forty years while our membranes and tapes have a life expectancy of 100 years.
Replicability:
We feel a key component of sustainability is simplicity and replicability and to this end we feel that our model and building methodology not only meets best practice criteria within the Irish construction sector but is easily replicated with the materials and skills available.
Carbon Footprint:
Independent calculations by carbon consultancy specialists Sustineo show that our system of build has a net carbon footprint. This means more carbon is stored in our structures than is emitted in the creation of the raw materials and products required to construct it. It compares very favourably with the log cabin and block built options, both of which have positive carbon footprints from the use of raw materials and products.
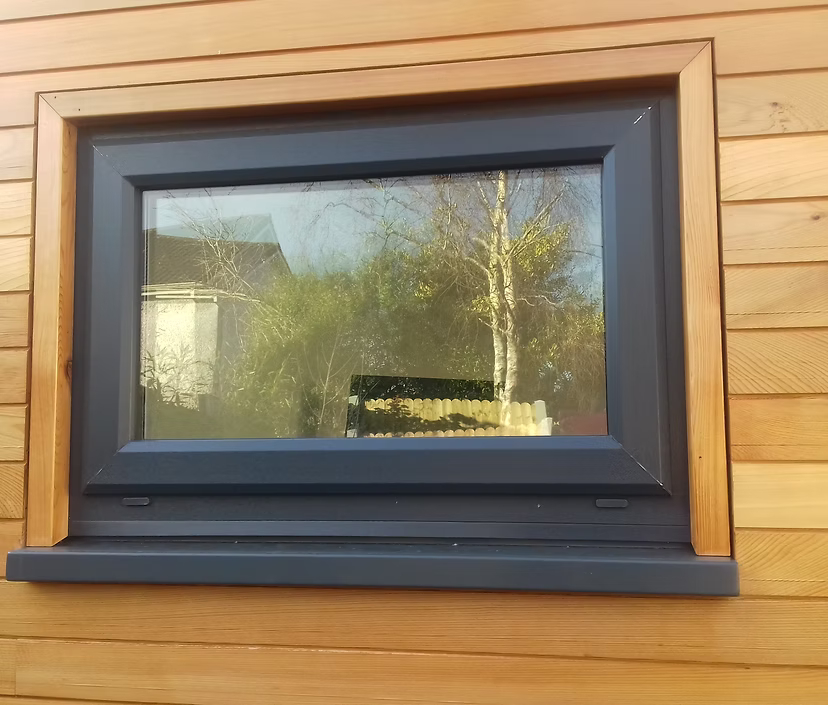
Low Carbon Footprint
Below are the results of a carbon footprint analysis applied to a 12m2 garden room. The data shows how BLUE MOUNTAIN’s system compares with a log-built version and a block built version.
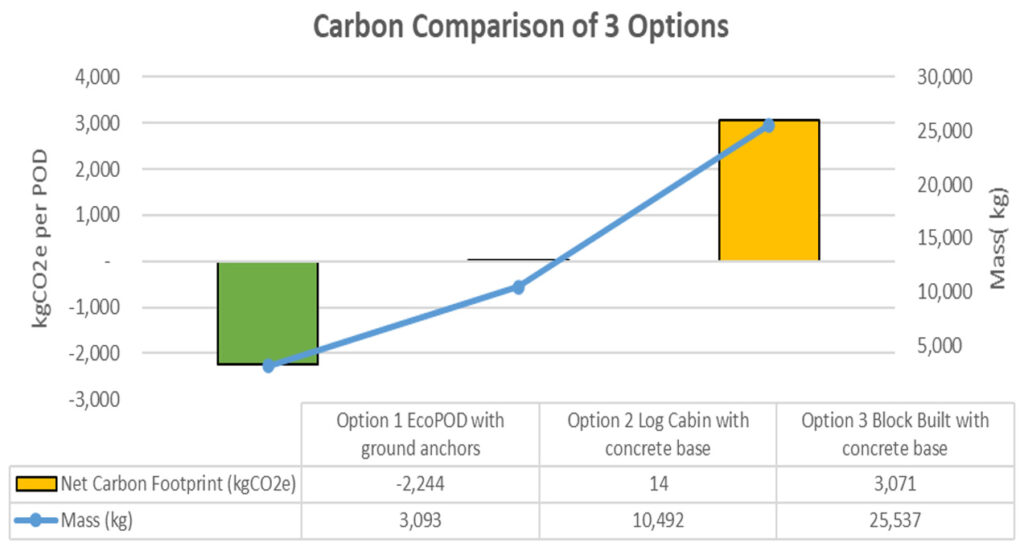
Calculations account for the embodied carbon of all the materials used in the construction of three options (base, walls and roof).
- 29% of the mass of a comparable log cabin with concrete base, resulting in a 71% material resource saving.
- 12% of the mass of a comparable block-built pod with concrete base, resulting in a 88% material resource saving.
- Our choice of materials have an embodied carbon footprint of 1,660 kgCO2e which is offset by the -3,900 kgCO2e stored in the biobased materials giving a net carbon footprint of -2,244 kgCO2e.
Into the Future
Our goal for next year which is currently in motion is to fit, as standard, environmentally friendly Marmoleum floor covering.
We would hope too, in the future, to change our internal finish which will completely remove the use of clean water out of the build process. We see this as our biggest, but not unsurmountable challenge.
BIO-DIVERSITY
Our wood products come from FSC managed forests which ensures the preservation of biological diversity.
Our pile system for footings is simple and requires no heavy machinery or digging. Unlike a concrete base the ground is undisturbed and the impact to adjacent flora and fauna is minimal.
An option we hope to make available to our customers in future is a green-roof build up which will replace the area taken over by the build.
ENERGY / WATER MANAGEMENT
We have almost totally eliminated the wet-trades from the build and associated use of processed water. The only area now using clean water is the skim finish internally.
We hope to replace this with a dry-lining process using tapered boards that require filler rather than a wet skim. Our only difficulty in making this switch is ensuring reliability and quality from subcontractors. At the moment we don’t feel confident in executing this without possible disruption to our schedule.
SUSTAINABLE TRANSPORT INITIATIVES
Timber is significantly lighter than concrete materials, making it easier and more efficient to transport. This reduced weight can lead to lower fuel consumption and decreased carbon emissions, supporting more sustainable transport practices.
Additionally, the ability to source timber locally can further minimize the environmental impact associated with long-distance transportation. When combined with modern logistics and eco-friendly delivery methods, such as electric or low-emission vehicles, the transportation of timber can contribute to a more sustainable construction industry.
LONG TERM IMPACT
The CO2 emissions from constructing and operating buildings are estimated to contribute around 39% of global CO2 emissions. The embodied carbon in our building materials alone contributes around 11% and may exceed 230 gigatons by 2060.
It is essential that we learn to understand where the hotspots are in the lifecycle of a building in order to address them. We believe that this model if emulated and enhanced could revolutionise the building industry and position it so it is set to meet the challenges and goals of a transition to a low carbon and sustainable society.